MEG-CM Type High Pressure Injection – Resin Transfer Molding Machine
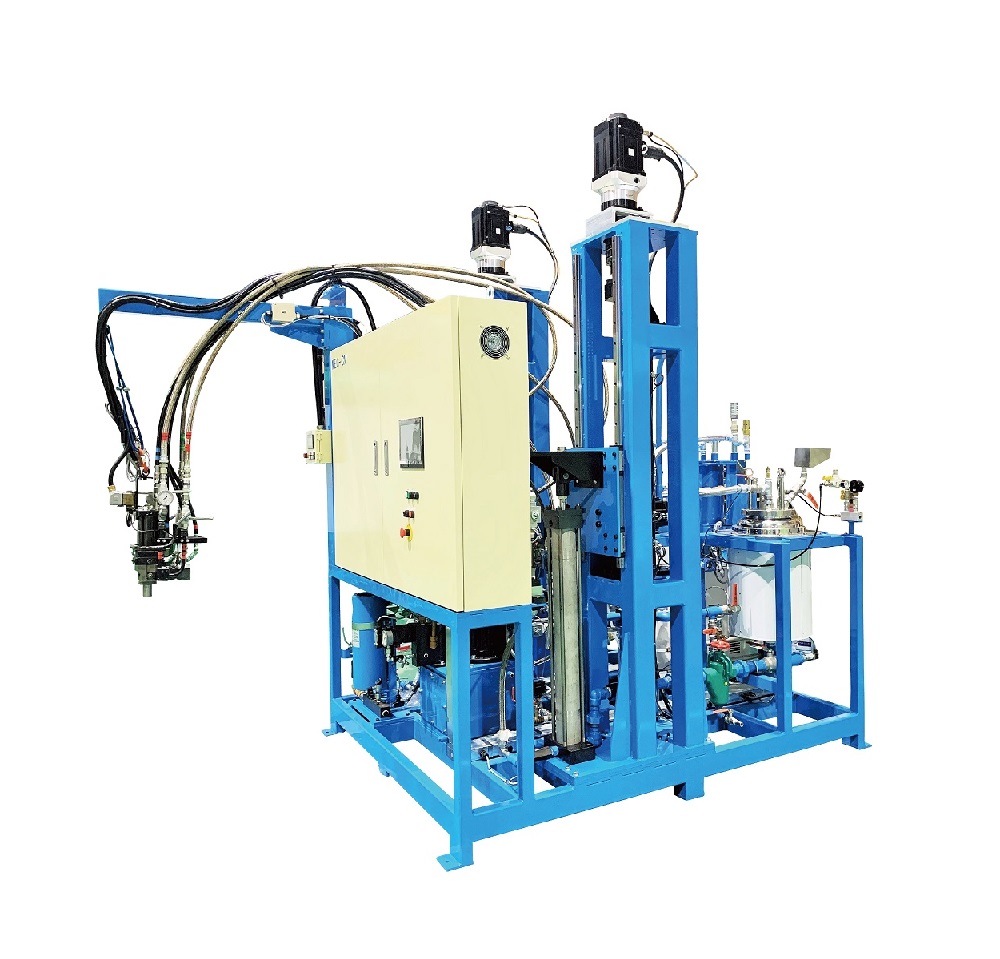
The MEG-CM Type CFRP Moulding HP-RTM Machine has been developed based on our accumulated knowledge and expertise in the high-pressure mixing technology over the years. This is a HP Injection machine equipped with the lathe cylinder metering unit specifically applicable for the CFRP molding.
MEG-CM Type Features
- A system in which resin (polyurethane, epoxy, etc.) is mixed and injected at high pressure into mold preset with carbon fiber or glass fiber to perform composite molding.
- Nylon injection compatible.
- It allows a large size mold manufacturing in a short time.
- It guarantees the TOP quality production molding supported by Mark type mixing head high precision mechanism.
- It comes with the latest model of the Production Constant Monitoring Control Panel to visualize the process.
- It has a highly accurate Temperature Control System (optional, up to MAX of 130℃)
- Its` well-thought and balanced design ensures effortless maintenance.
- It suits two types of mixing head, MEG-MARK-R and MEG-MARK-VII (depends on the application)
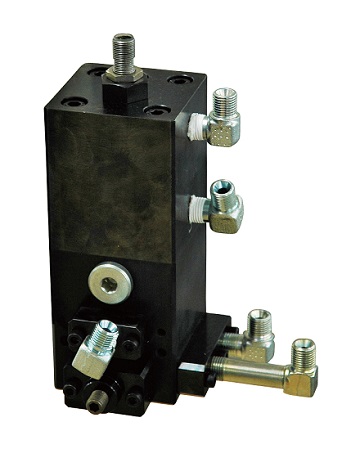
Mixing Head Mark-R
Essential part of the MEG-ACMA Polyurethane High-pressure Foaming Machine
Mark-R is a top-performer 2-component high-pressure RTM specialized mixing head that represents our extensive knowledge and far-reaching competence in the field. It delivers premium quality molded products with an exceptionally accurate discharge rate and a perfect blend.
- Direct injection enables well-defined metering of the raw materials
- AIR – FREE raw materials upon injection
- Outstanding durability – made of special steel
- Exclusive design seal system prevents internal backflow
- The joint tower between the mixing block and hydraulic cylinder acts as the debris shield during cleaning shaft operation
- Distinctive surface finishing & unique coating stop the leakage, and there is no fear for the burn-in lock during operation
- The DOP cup prevents the cleaning shaft & discharge orifice raw material retention/ adhesion
- The minimum discharge time is ONLY 0.1 sec
- The assorted size mixing heads are available (suits a wide range of discharge volume small to large)
- Simple design – easy maintenance
- Compact and portable – easy to handle
- Cost-effective performance – low number of consumables
- Built-in electric heater within the mixing block enables to keep the discharge raw material temperature extremely accurate
- Built-in pressure sensor on the supply side of the mixing block helps to control strictly discharge pressure
- Can be easily attached to the mold with a dedicated bracket
Mixing-head “MARK –Ⅶ type
Highly functional and versatile device an upgraded version of our prototype Mark-III developed and marketed in 1977. This innovative equipment facilitates a wide range of applications and impresses with its perfectly accomplished flow system.
|
![]() |
Always operate in the best condition by visualization system
①Trouble shooting function | |
When an error occurs, the troubleshooting guidance information is automatically displayed on the touchscreen monitor. User would be able to understand and solve the cause of error within a short time. | ![]() |
②Maintenance time notification function | |
Based on the operational time of each piece of equipment and the number of shots, the maintenance time notification, as well as consumable parts replacement timing, would appear on the touchscreen panel. This notification system ensures timely maintenance to achieve a stress-free and smooth operation. | ![]() |
③Operation monitoring function | |
One should constantly monitor the operation status of each device displayed on the touchscreen panel (a standard type includes raw materials temperature, cylinder pump speed, etc. parameters.). Optionally, raw material flow rate and circulation status, discharge pressure indicator and more could be offered. |
![]() |
The types of MEG-CM and Specifications
Type |
Material-A : Material-B (100:100) |
Material-A : Material-B (100:50) |
||||
---|---|---|---|---|---|---|
Min pump |
Max pump |
Electric power(KW) 3phase 200V |
Min pump output |
Max pump output |
Electric power(KW) |
|
MEG-CM-10 | 40cc/sec | 200cc/sec | 21.5Kw | 30cc/sec | 150cc/sec | 21.5Kw |
MEG-CM-30 | 120cc/sec | 600cc/sec | 24.5Kw | 90cc/sec | 450cc/sec | 24.5Kw |